Secret Benefits of Using Plastic Injection Molding in Production
Plastic shot molding has actually emerged as a critical method in the manufacturing industry, providing a range of advantages that considerably enhance production procedures. Remarkable advantages consist of amazing production efficiency, the capacity for detailed layouts, and a positive expense structure that appeals to businesses of all dimensions.
High Manufacturing Effectiveness
One of the most substantial advantages of plastic injection molding is its high manufacturing effectiveness, which can result in the quick manufacturing of thousands of the same parts within a short duration. This effectiveness is largely credited to the automatic nature of the injection molding procedure. Once the preliminary configuration and mold production are completed, the manufacturing of parts can be scaled up significantly without an equivalent boost in labor costs or time.
The procedure usually involves home heating plastic pellets until they thaw, injecting the molten product into an exactly designed mold and mildew, and allowing it to solidify and cool down - Plastic Injection Molding. This cycle can be completed in mere secs to minutes, depending upon the complexity and size of the component being produced. Therefore, manufacturers can accomplish high output rates, making plastic shot molding a perfect selection for automation
Moreover, the ability to create huge amounts regularly makes certain lower unit expenses, making it an economical solution for companies. This manufacturing efficiency not only satisfies market needs promptly but likewise boosts the total competitiveness of makers in numerous sectors. Consequently, plastic injection molding stays a recommended approach for high-volume manufacturing applications.
Layout Flexibility
The capabilities of plastic injection molding expand past high manufacturing performance to incorporate considerable style versatility. This manufacturing process permits developers and engineers to create intricate and complex forms that may be difficult or impossible to achieve with various other approaches (Plastic Injection Molding). The capability to quickly adjust and customize mold designs suggests that makers can swiftly react to transforming market needs and innovate brand-new item designs without comprehensive retooling
Moreover, plastic shot molding supports a variety of materials, consisting of different thermoplastics and thermosetting polymers. This variety makes it possible for the manufacturing of components with one-of-a-kind homes, such as enhanced stamina, lightweight attributes, or particular thermal and electric characteristics. In addition, the process permits the assimilation of multiple functions into a solitary part, minimizing the need for setting up and minimizing prospective factors of failure.
The accuracy of injection molding likewise ensures that elements are generated with tight resistances, boosting fit and function. The versatility to produce little to huge batches effectively better underscores its versatility, making it an ideal option for both prototyping and large production. Generally, layout flexibility is a foundation benefit of plastic shot molding, driving innovation in many sectors.
Cost-Effectiveness
Cost-effectiveness stands out as a considerable advantage of plastic shot molding in manufacturing. This process enables for the automation of top quality plastic elements at a fairly reduced price each, particularly when compared to other producing techniques. The performance of shot molding hinges on its capacity to generate complex shapes with minimal waste, enhancing material usage and minimizing general costs.
In addition, the rate of manufacturing is a critical consider cost-effectiveness. Once the initial mold is created, the moment called for to generate each succeeding component is substantially minimized, causing boosted outcome and faster turnaround times. This rapid production capacity not just fulfills high-volume needs but additionally lessens labor costs, as automated systems can handle much of the procedure.
In addition, the durability and long life of injection-molded items add to their cost-effectiveness in time. These components usually call for much less maintenance and substitute, leading to lower lifecycle costs for end-users and producers alike. In recap, the cost-effectiveness of plastic shot molding makes it an attractive option for organizations seeking to enhance their production effectiveness while maintaining product top quality.
Material Versatility
Product flexibility is a hallmark of plastic shot molding, enabling suppliers to choose from a wide variety of polymers that meet details performance needs. This versatility enables the production of parts tailored to numerous applications, ranging from vehicle parts to customer items.
Typically made use of materials consist of acrylonitrile butadiene styrene (ABS), polycarbonate (COMPUTER), and polypropylene (PP), each offering unique buildings such as effect resistance, warmth tolerance, and chemical security. Suppliers can choose products based upon characteristics like toughness, weight, and thermal stability, guaranteeing completion product satisfies useful and aesthetic needs.
Additionally, the capacity to incorporate various polymers via co-injection techniques further improves product versatility. This permits the production of multi-layered components with distinct attributes, such as soft-touch surface areas incorporated with rigid structural aspects.
Furthermore, innovations in biodegradable and recycled materials are broadening the choices readily available, straightening with sustainability objectives in manufacturing. Overall, the diverse material choices in plastic shot molding equip suppliers to introduce and maximize their items, promoting the development of highly specialized and competitively advantageous solutions.
Enhanced Product Durability
Improved product sturdiness is among the considerable advantages offered by plastic injection molding, as the production procedure enables for exact control over material residential properties and element style. This precision ensures that the last items my explanation display enhanced mechanical strength and strength, which are important consider a series of applications, from durable goods to commercial elements.
Furthermore, the complex geometries possible via injection molding enable the development of parts that can withstand tension and pressure far better than traditional manufacturing techniques. The uniform wall density and minimized product waste additionally add to the total integrity of the product, minimizing the possibilities of failing throughout its lifecycle.
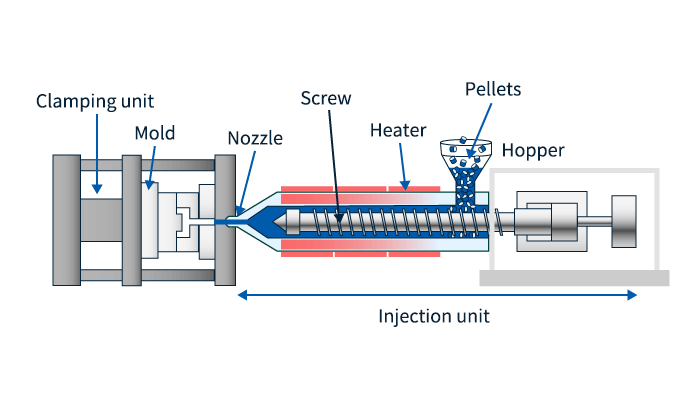
Final Thought
In final thought, plastic shot molding presents considerable benefits in manufacturing, including high manufacturing performance, design versatility, and cost-effectiveness. These factors collectively develop plastic shot molding as view website an optimal service for mass manufacturing applications, resolving the dynamic requirements of modern-day production environments.
Plastic injection molding has actually arised as a pivotal method in the production field, offering a range of advantages that dramatically boost production processes.One of the most considerable advantages of plastic shot molding is its high manufacturing performance, which can result in the quick production of thousands of identical parts within a short timeframe. Plastic Injection Molding.The capabilities of plastic injection molding prolong beyond high check these guys out production effectiveness to include considerable layout adaptability.In verdict, plastic shot molding offers substantial benefits in production, consisting of high manufacturing effectiveness, style versatility, and cost-effectiveness. These elements collectively establish plastic injection molding as an optimal solution for mass manufacturing applications, resolving the vibrant demands of contemporary manufacturing atmospheres